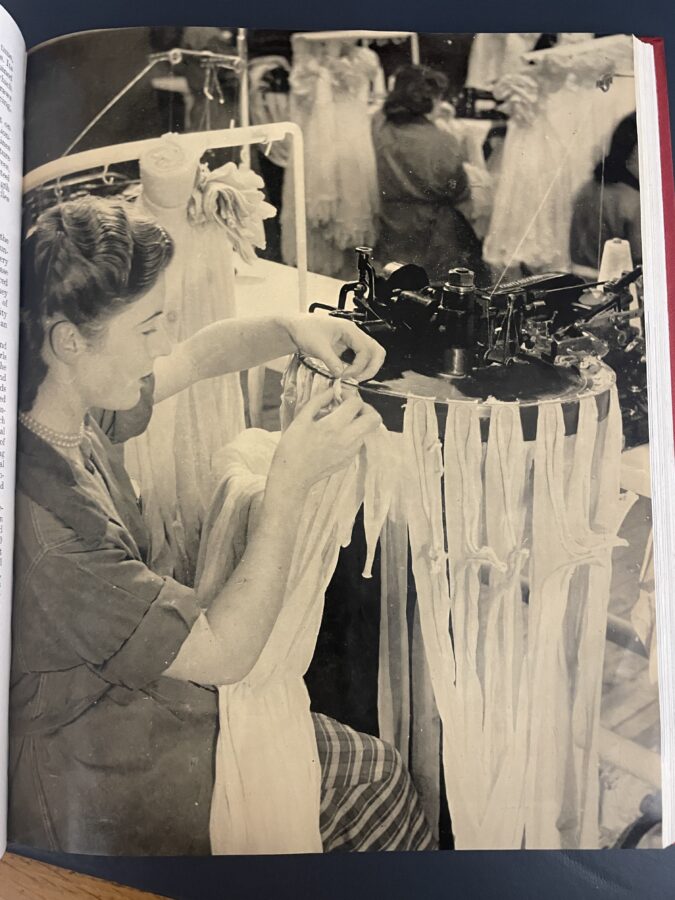
Kieran’s Our City, Our Town Article,
Cork Independent, 28 November 2024
Making an Irish Free State City – Sunbeam Wolsey and the Nylon Evolution
In an article in the Journal of the Association of Chambers of Ireland in July 1953, a write up on Sunbeam Wolsey Ltd reveals the company’s foray into the production of nylon stockings.
When the big American firm of Du Pont announced that they were about to produce a new synthetic fibre, nylon, in commercial quantities, the world took little notice in the late 1930s. For another thing, war (second World War) was imminent. When nylon came it surpassed all expectations and claims and it more than repaid for the ten years of research work and expenditure of many millions of dollars that produced it.
When the concept of nylon appeared on the market, Sunbeam Wolsey Ltd was one of the first to see the possibilities of the new filament. Although wool was the main product of Sunbeam Wolsey, they had ample room for expansion. The company sent its technicians America to study it in all aspects of nylon’s production and manufacture. They returned to Cork enthusiastic about its future. The result was that as soon as nylon became freely available just after the war, in 1947, Sunbeam installed the latest American machinery and began to make nylons.
There was the choice of having the operators trained at home or by practical demonstration and experience in the United States. A group of workers was sent to study the methods used at the famous Berkshire Mills in Reading, Pennsylvania. They worked there for periods ranging from six to twelve months, side by side with the skilled American technicians.
The nylon yarn used in the Cork mill was imported from Du Pont and from British Nylon Spinners. Using American methods and processes throughout, Sunbeam learned to produce nylons identical in quality and appearance with the best American product. Indeed, the first quality Sunbeam stockings retailed at a lower price than similar American stockings did in their home market.
In the Cork mill yarn for nylon was wound onto bobbins or pirns, which were mounted on fully-fashioned hosiery machines. The whole section of the factory was not only self-contained, but sealed off by double doors from the other sections. The delicacy of the yarns used and their response to the slightest alteration in temperature or humidity made it essential that both these factors had to be maintained at a constant level. For this reason an air conditioning system guarded against any deviation from 80 degrees Fahrenheit throughout the department and a relative humidity of 50 per cent.
Before it could be knit in the machines, the yarn had to be strengthened by receiving a coating of size. This in turn created more difficulties because of the roughness of the treated yarn, which had to be given a certain degree of malleability by immersion in another solution before it became tough enough to withstand the rigours of the knitting and supple enough to link in the form of the stitches without fraying. The Journal noted of the machinery used:
“Stretching a full 53 feet from end to end, the hosiery knitting machine is one of the marvels of the modern world. Unerringly, once set in motion, it performs amazing feats of skill starting the stocking at the top or welt in heavily reinforced material, doubling the welt over and picking up all the stitches again simultaneously, changing down to the finest of yarn, and knitting the almost invisible web of stocking, dropping stitches to shape the knee, calf and ankle, drawing in more yarn to reinforce the heel, and finishing the stocking by dropping more and more stitches until the foot ends at the toe”.
With 12,000 needles working to regular clock-like rhythm, the machine knitted 30 stockings at a time, each run took about 45 minutes; Its movements were pre-determined through an electronic brain, which counted the stitches, casted off, drew in the extra yarn for reinforcing and guided the flashing needles.
Not only is the yarn dependent on strict air and temperature conditioning of the department; the machines were delicate too. If the temperature were to vary by only a few degrees, the consequent expansion of the steel bars that ran the whole 53 feet length of the unit would throw the needles far out of alignment.
The stockings were knitted in the flat opened-out form and of un-dyed yarn. These blanks were very susceptible to snags, and to increase their resistance they were first placed in a conditioning chamber where they are submitted to a temperature of 164 degrees and a relative humidity of 70 per cent for a period of half an hour. Afterwards they were dried and taken to the seamers. The formed stockings were then tested and examined on an expanding tube; “The depression of a foot pedal by the operator exerts a pressure of about 30 lbs, stretching the stocking to more than twice its normal diameter. Any faults will show immediately under such a test, and faulty stockings are discarded”.
The next process was that of pre-boarding. The stockings were drawn over flat leg-shaped metals and placed in a steam oven at about 30 lbs pressure for five minutes to set the stitches, which afterwards would never lose their shape. They were then scoured in a large washing machine to remove the “size still coating the yarn”. After drying the bags were placed in a rotating drying machine and subsequently dried in centrifugal hydro-extractor.
The final manufacturing process involved the stocking once again drawn over leg shaped flat metal pieces, which carry them through another oven chamber in which the shape of the stockings is fixed permanently. They were then laid in heaps of one dozen and moved away by conveyor belt to the packing department, which they were checked for faults and then onto the packers.
All the cardboard boxes used for Sunbeam products were made at the factory, where a complete box-making plant was installed, operators and all, some years previously. There was also a huge dispatch department, from which the many products were sent to the wholesale warehouse in Dublin, from where the entire country, except Cork City and County, was served. Sunbeam was selling more and more goods abroad. Twice a year, buyers from New York’s largest stores travel to Europe seeking the best goods available to bring home to their customers.
Caption:
1281a. Employee at Sunbeam Wolsey Ltd working on nylon stockings, 1953 (source: Journal of the Association of Chambers of Ireland, July 1953; British Library).